Faculty: Pablo Moyano Fernandez
Our team designed a concrete panel that can be modulated to form the building enclosure of a seaside pavilion. The natural gradient of the panel draws inspiration from the waves at the beach. The cut-outs within each panel function as ventilation and for water to pass through. At night, the pavilion can be illuminated like a lantern on the beach.
In partnership with Gates Precast and the PCI Foundation, a full-scale (6'x12') mockup was fabricated at the plant. CNC milling and 3D printing were utilized to assemble the complex geometries of the mould.
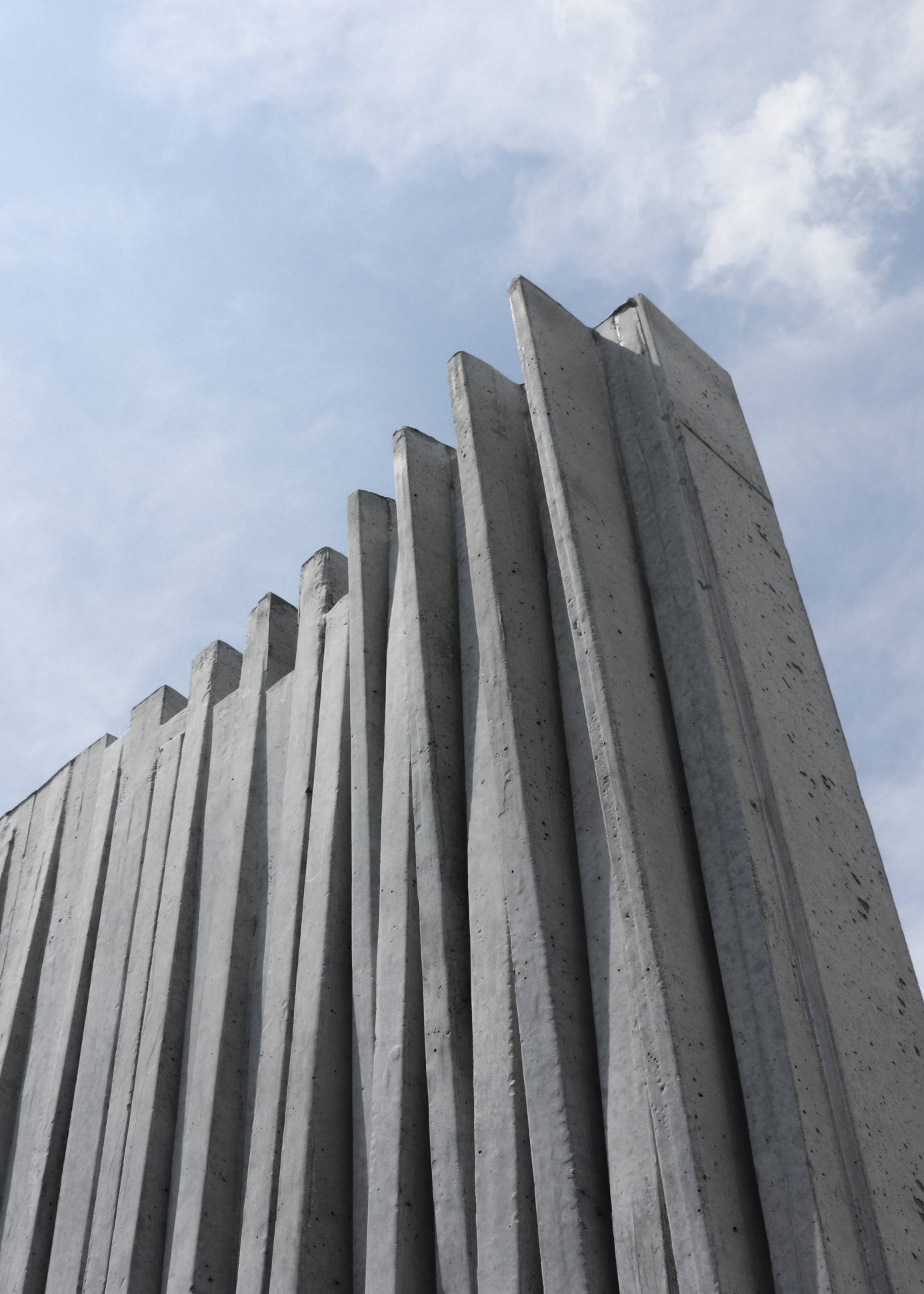
Gradient
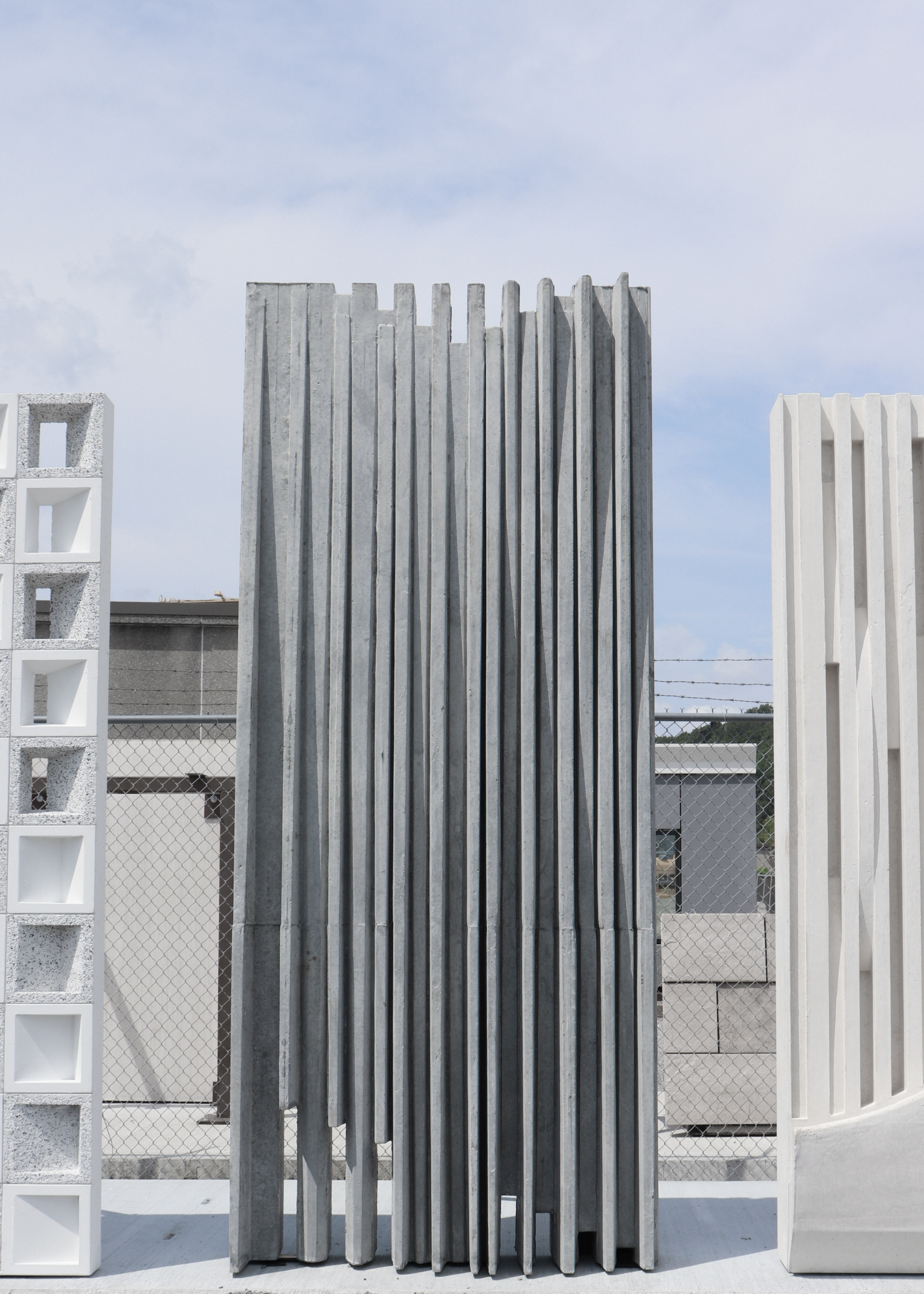
Front
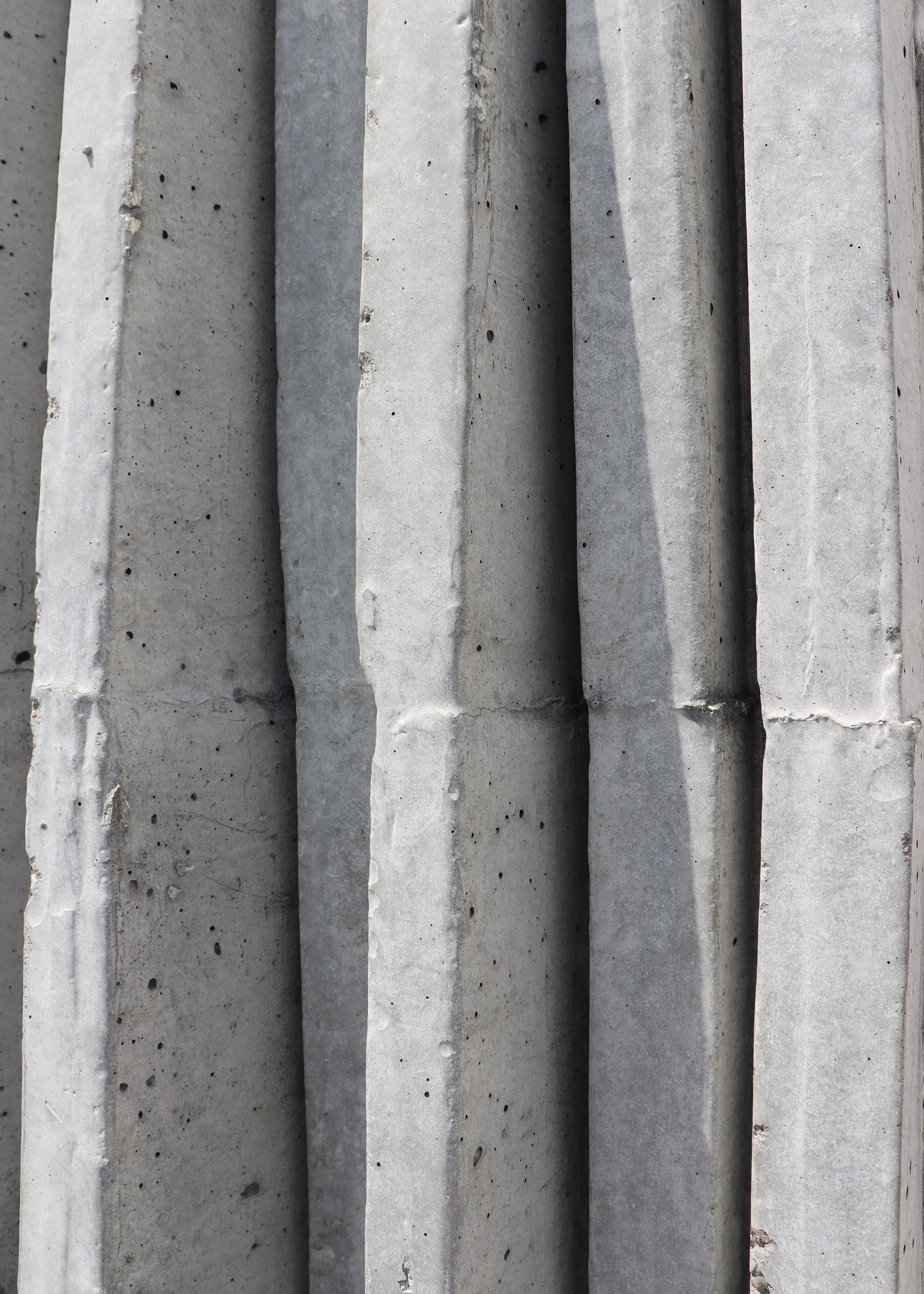
Texture
Full-scale Concrete Panels
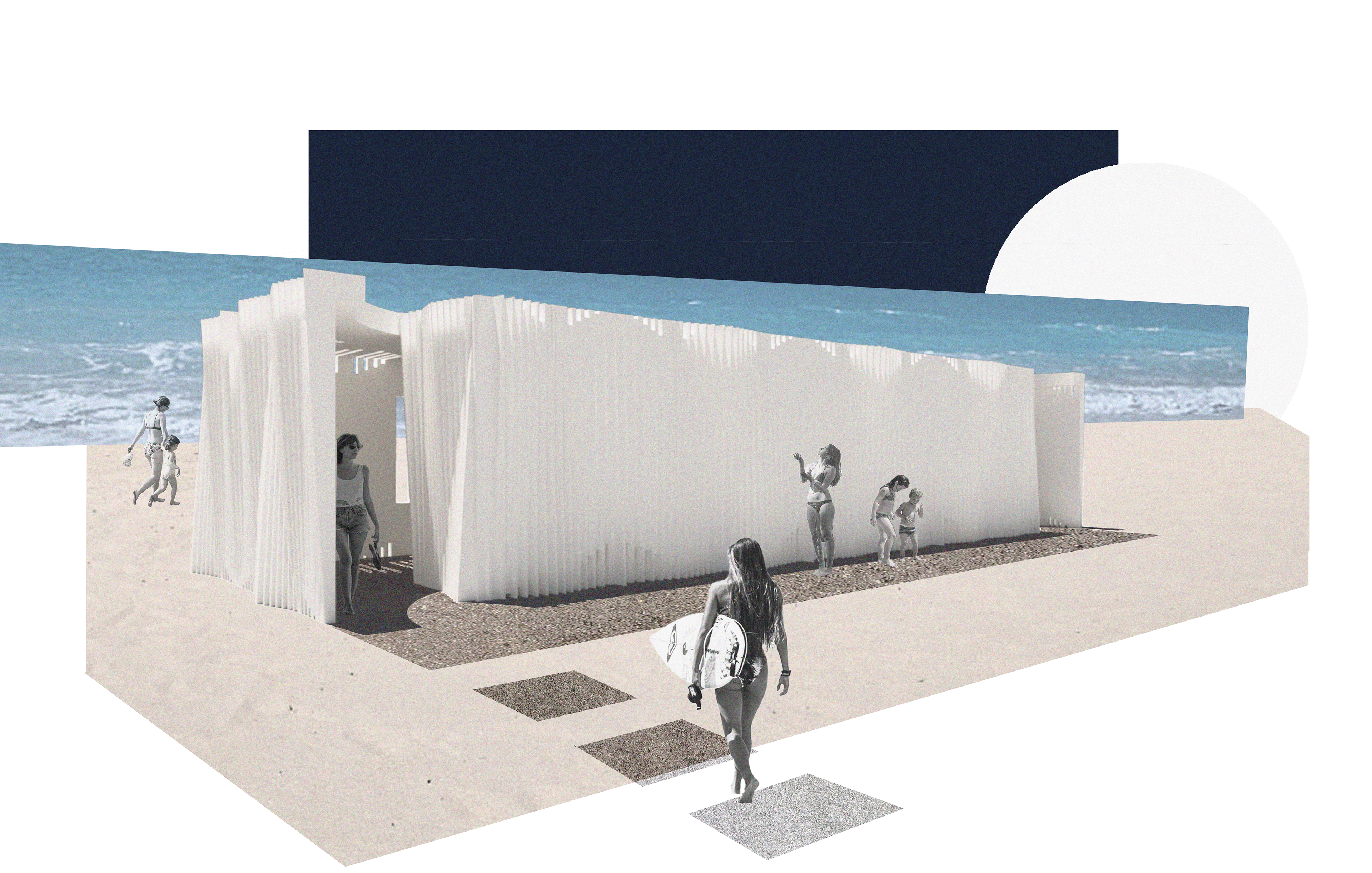
Rendered Collage
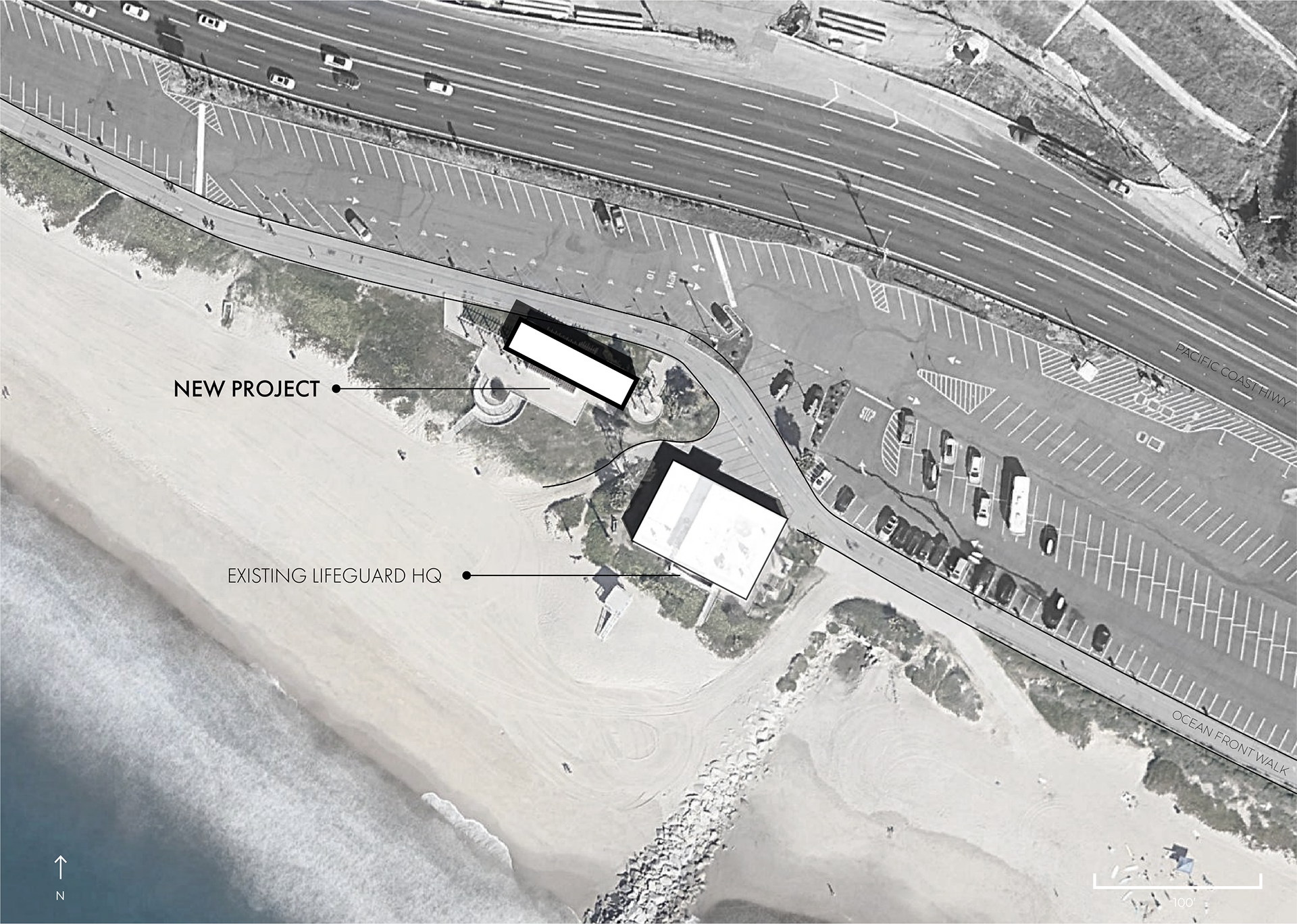
Proposed Site
LOCATION
Ocean Front Walk
Pacific Palisades
California
Pacific Palisades
California
AREA
900 - 1000 SF
PROGRAM
Public Bathroom
Showers
Change rooms
Showers
Change rooms
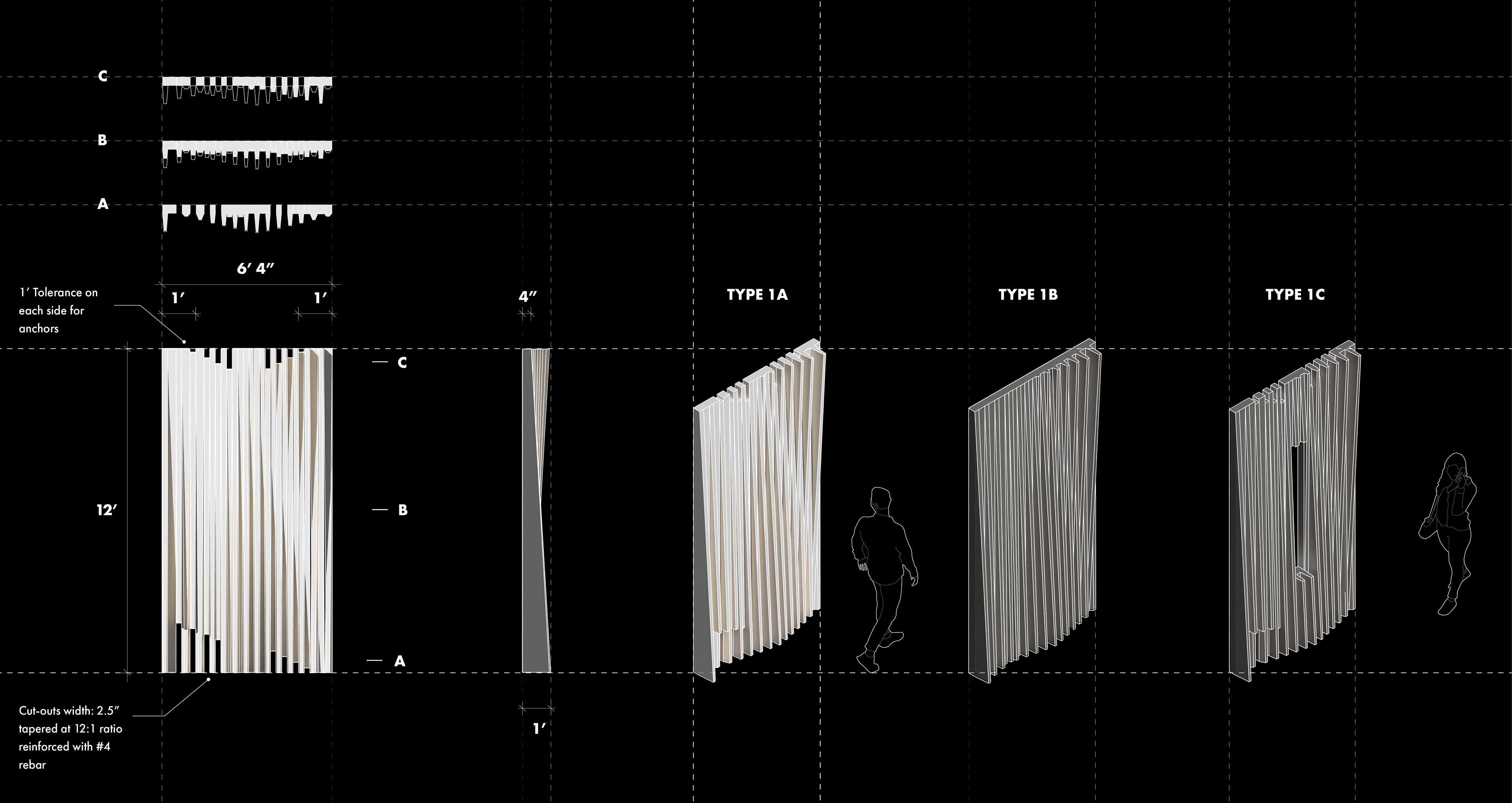
Panel Dimension + Types
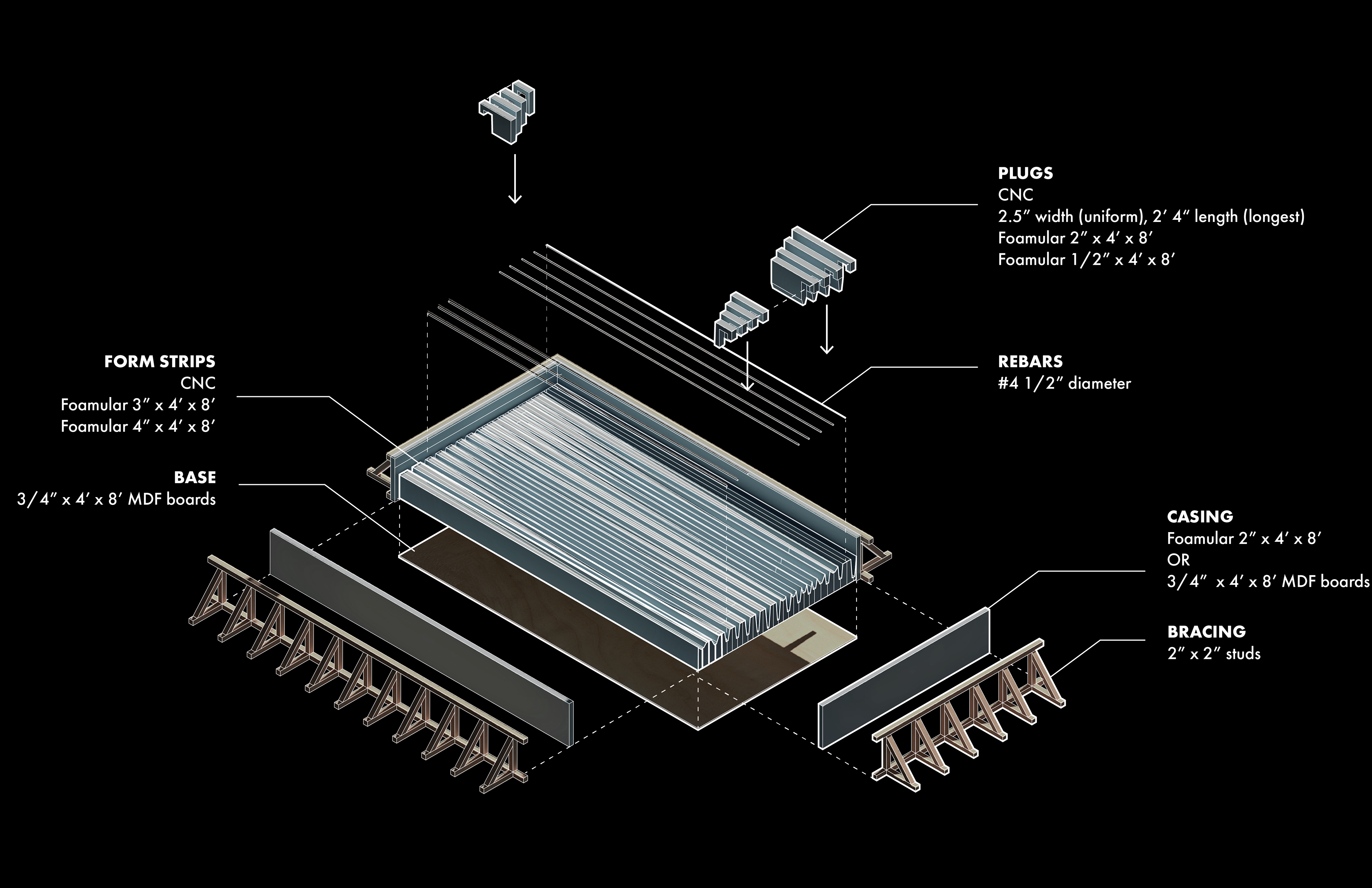
Formwork Design
Process
The mould was segmented into 40 strips of different profiles to be cut by the CNC. After the strips were glued together, joint compound and resin were applied to the surface for a smoother finish. The foam mould was then transported to Gates Precast to be reinforced with kickers and rebars. The anchors allowed the panel to be lifted outside for demoulding.
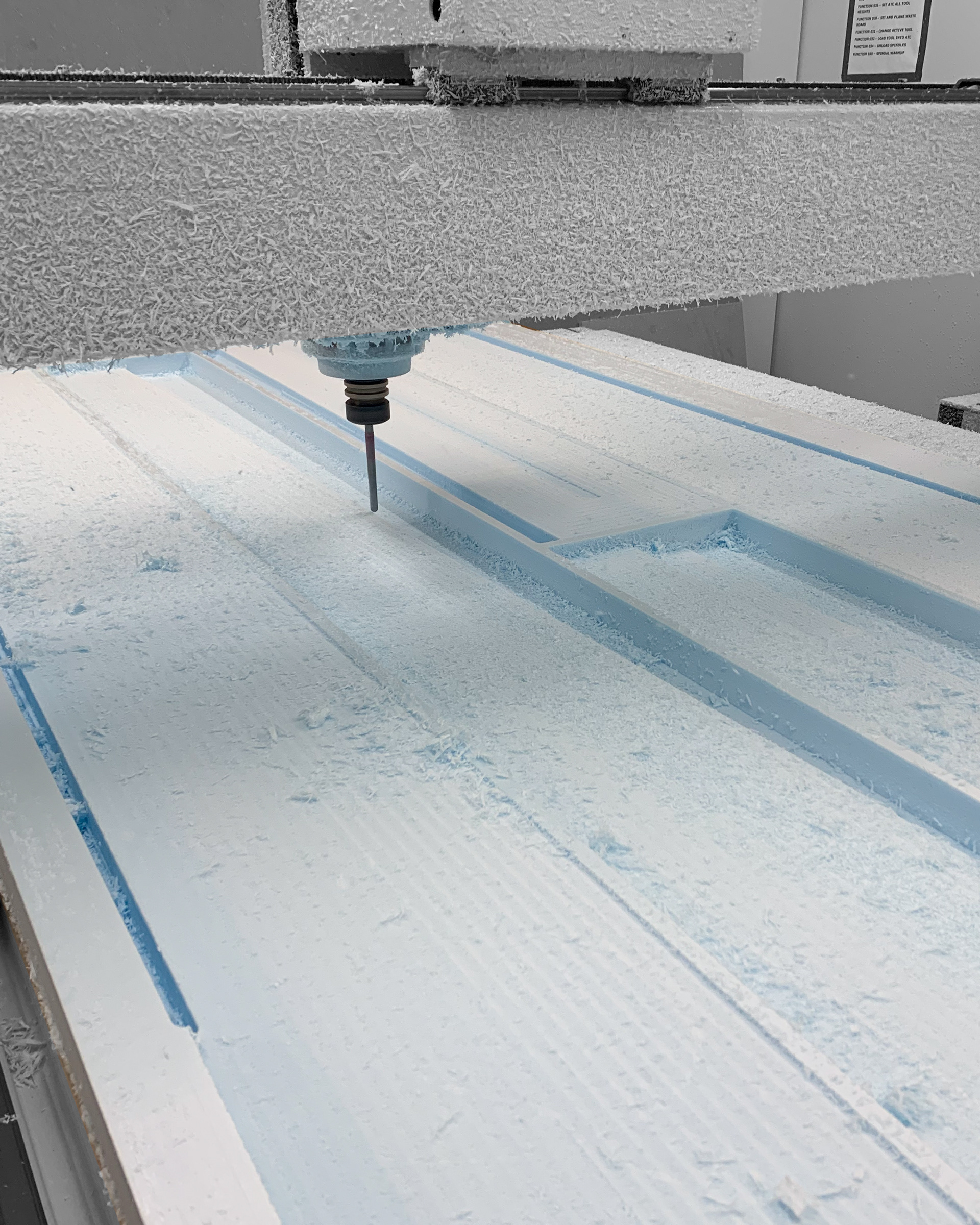
CNC Routing
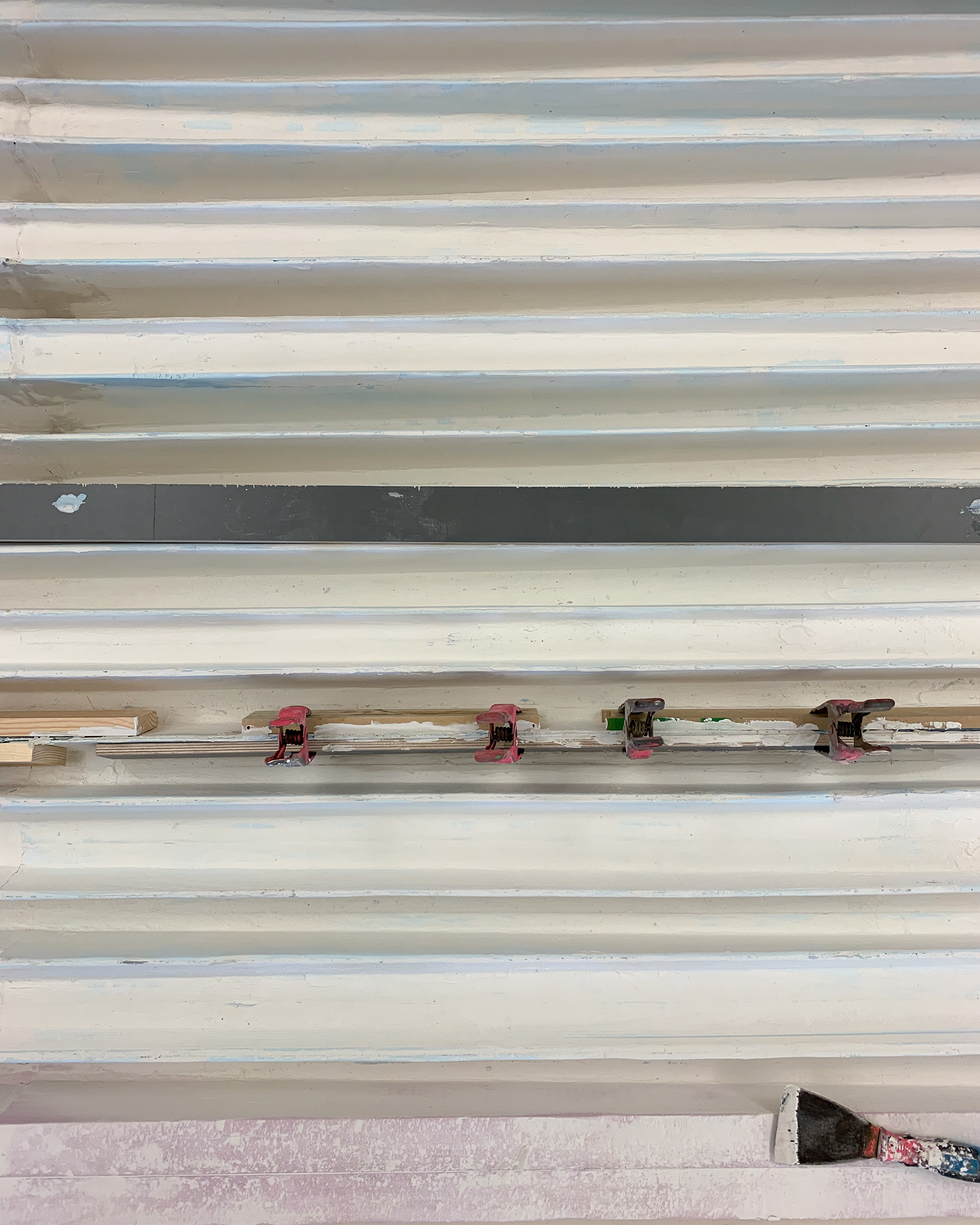
Assembly
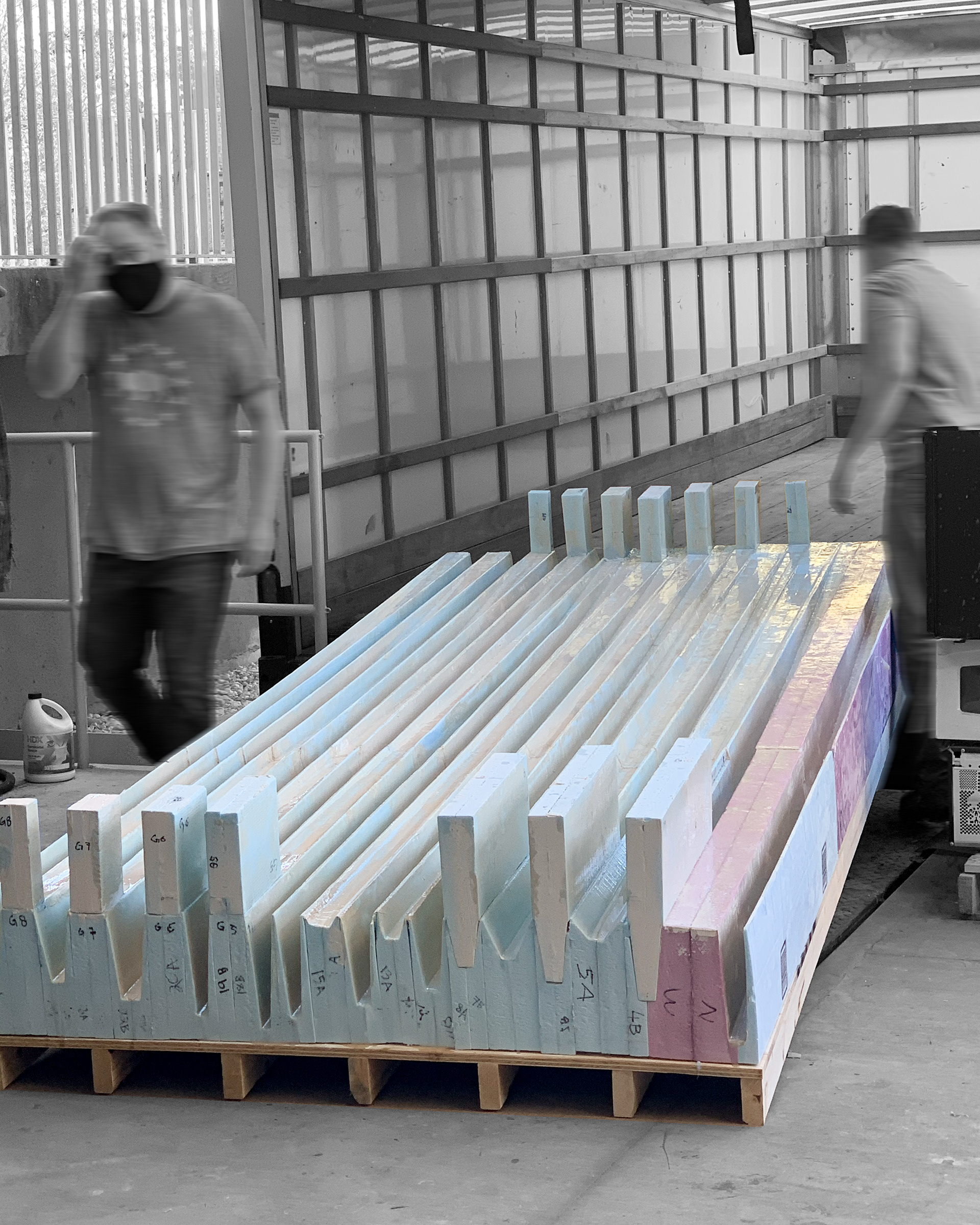
Transportation
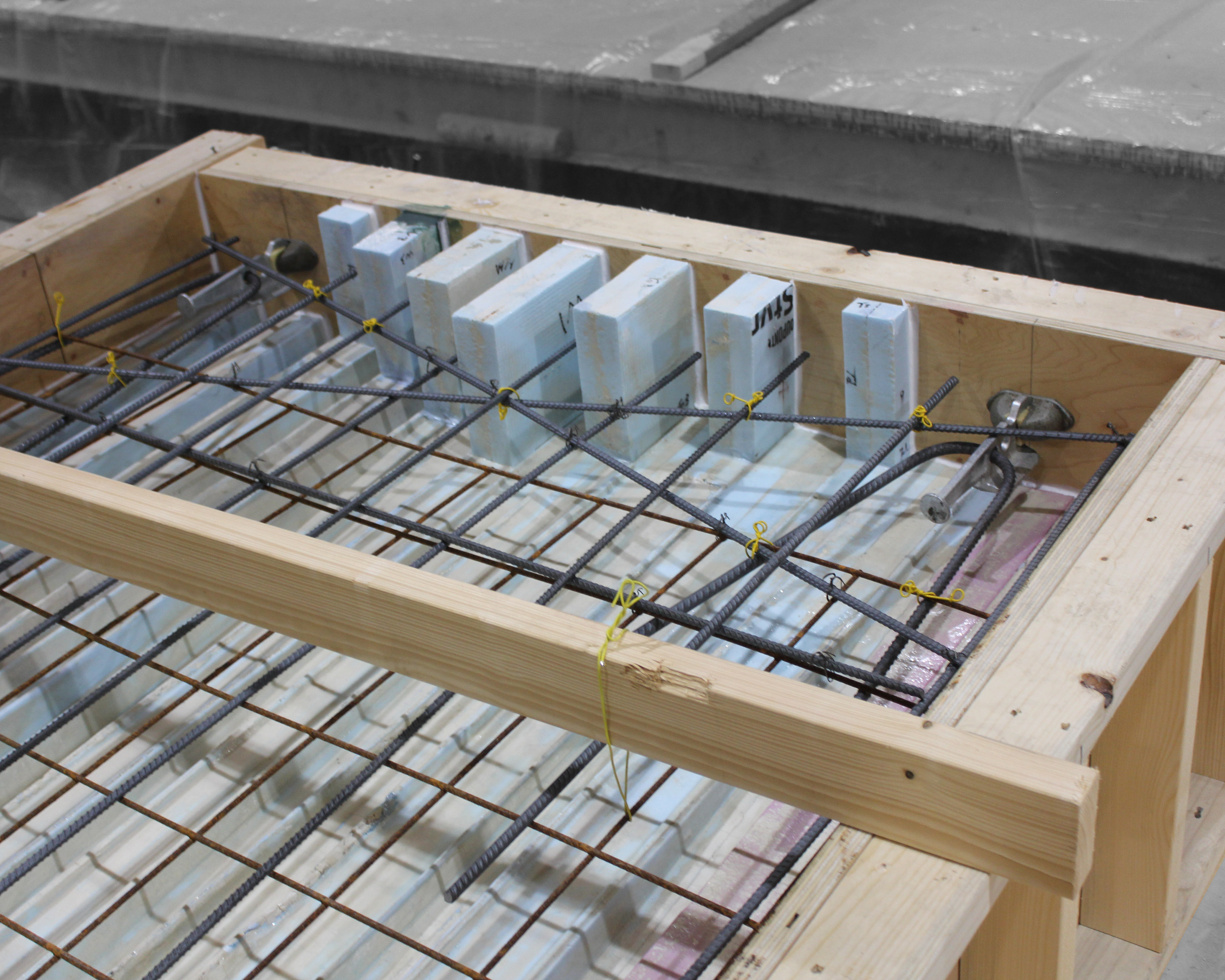
Rebar + Supports
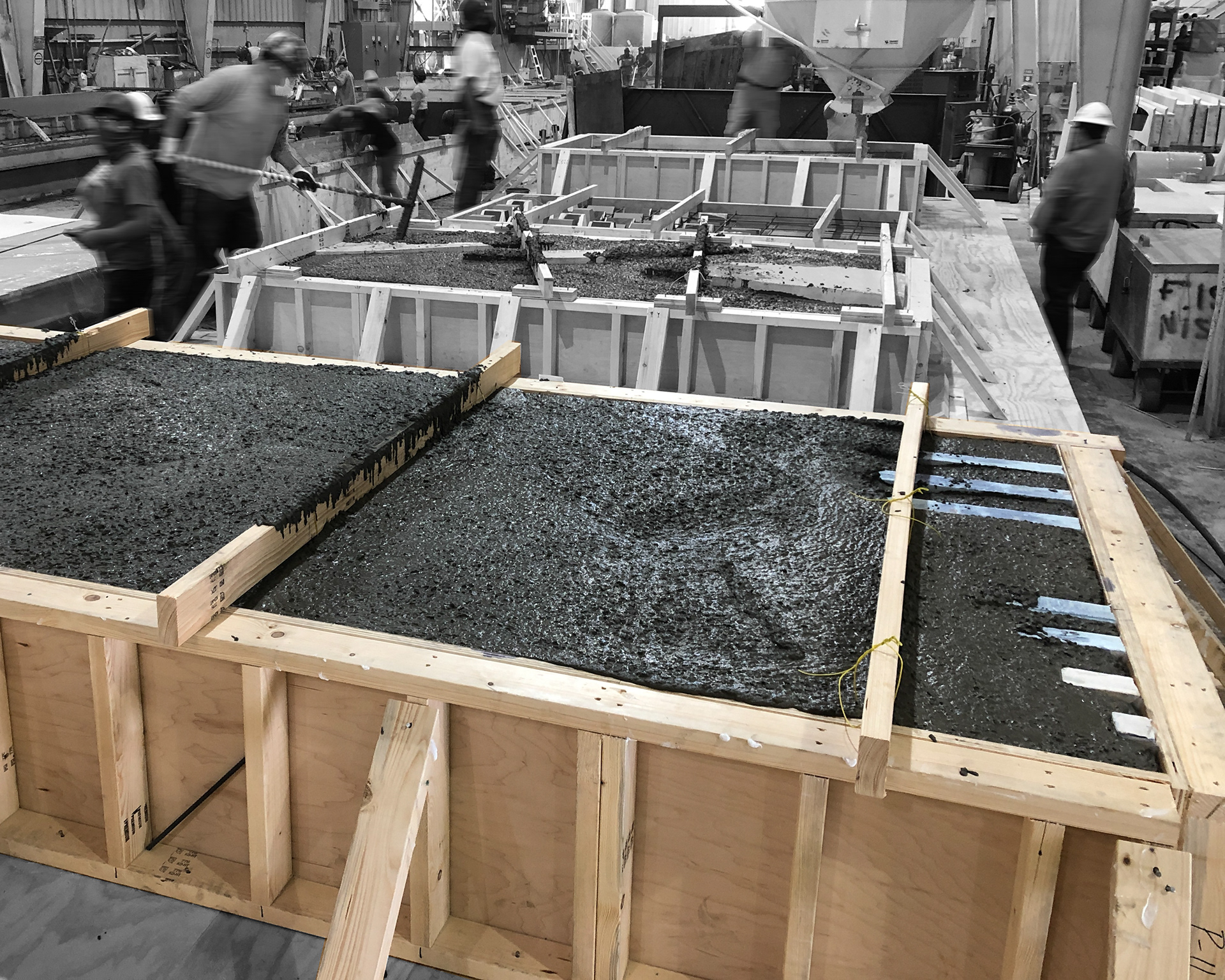
Concrete drying
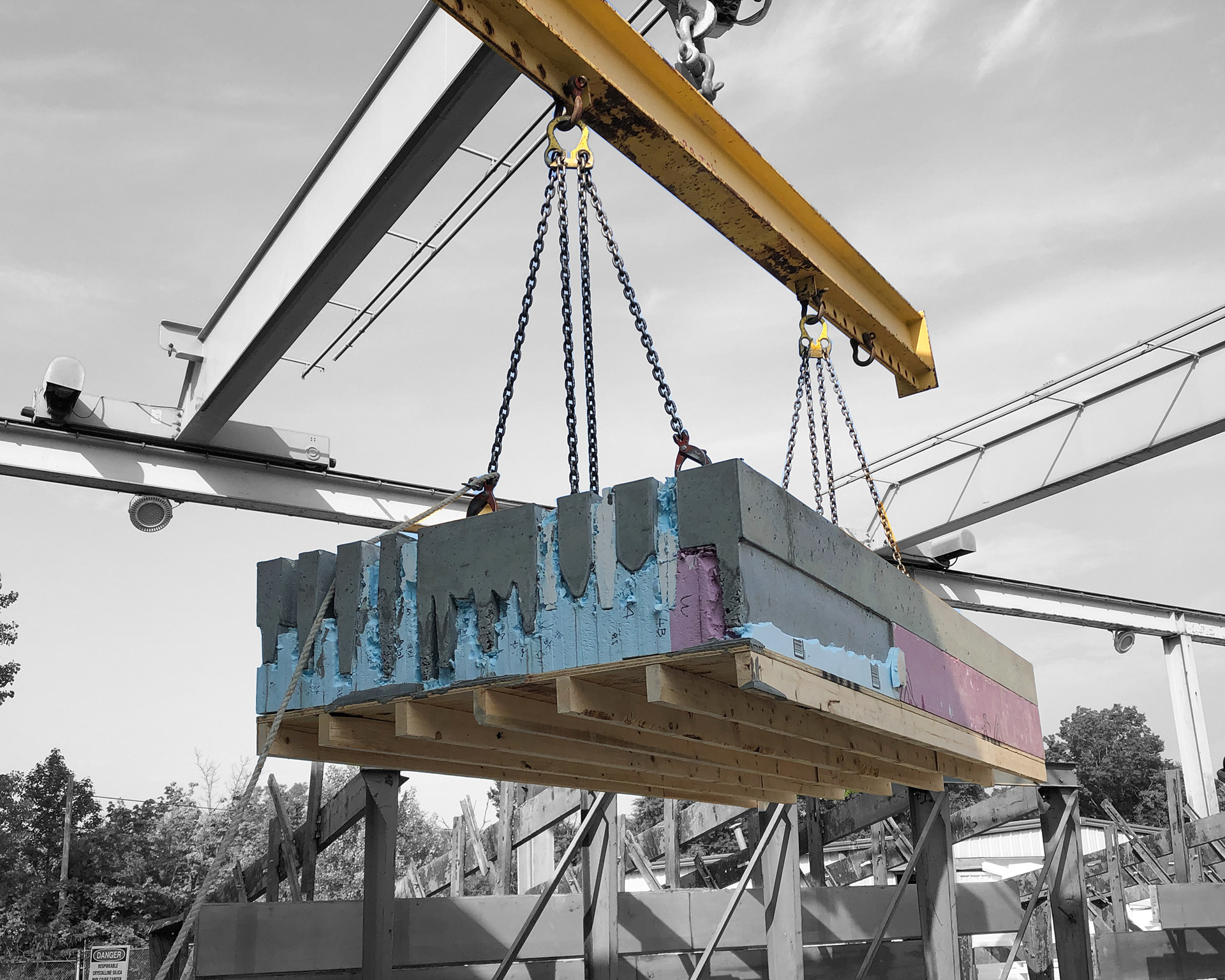
Lifting by crane
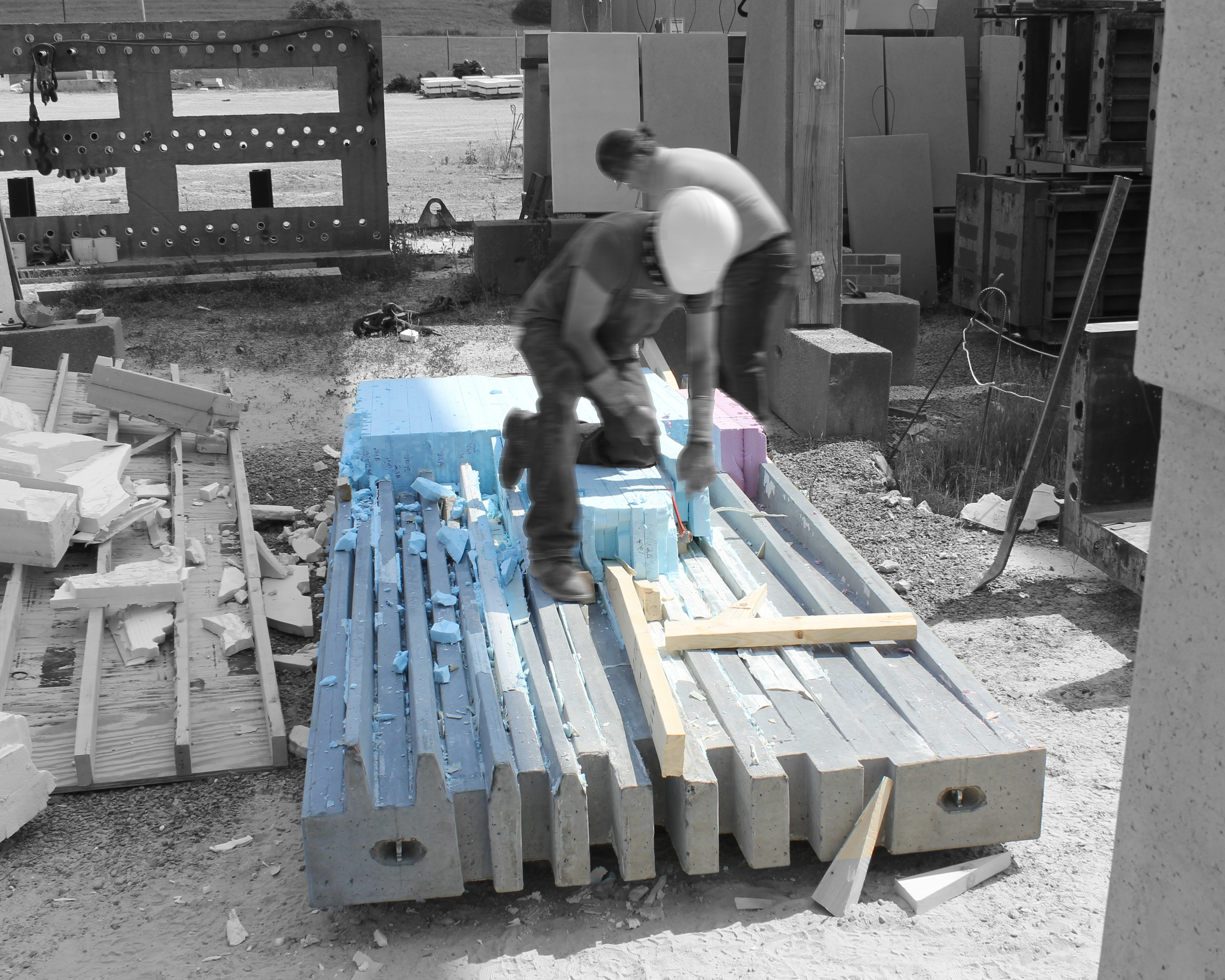
Mould stripping
Timeline
The research and design phase lasted 8 weeks. The mould-making process took 4 weeks for my group of 3. The casting was done at the Gates Precast plant, taking 24 hours to pour the concrete and for it to dry. The demoulding process took another 24 hours.
Pouring Concrete
Lifting Panels
Group Credits
Panel Design: Meredith Busch, Lisa Chen
Drawings/Renderings: Lisa Chen
Photography: Lisa Chen, Cody Xie